How Motivo Tackles Hydrogen Complexity
- Motivo
- Apr 16
- 2 min read
In 1966, GM unveiled the first hydrogen fuel-cell vehicle, the Electrovan. Since then hydrogen has remained in discussion as a potential path to clean renewable energy for mobile platforms.. Hydrogen is used in several key industrial processes, so large investments are being made into cleaner, safer and more cost-effective production, storage and transportation of Hydrogen. Applications like aviation, locomotives and long-haul shipping stand to benefit from those investments. It’s not likely that Hydrogen will replace battery-electric any time soon, but it does have the potential to play a key role in solving some of the remaining challenges with battery-electric systems.
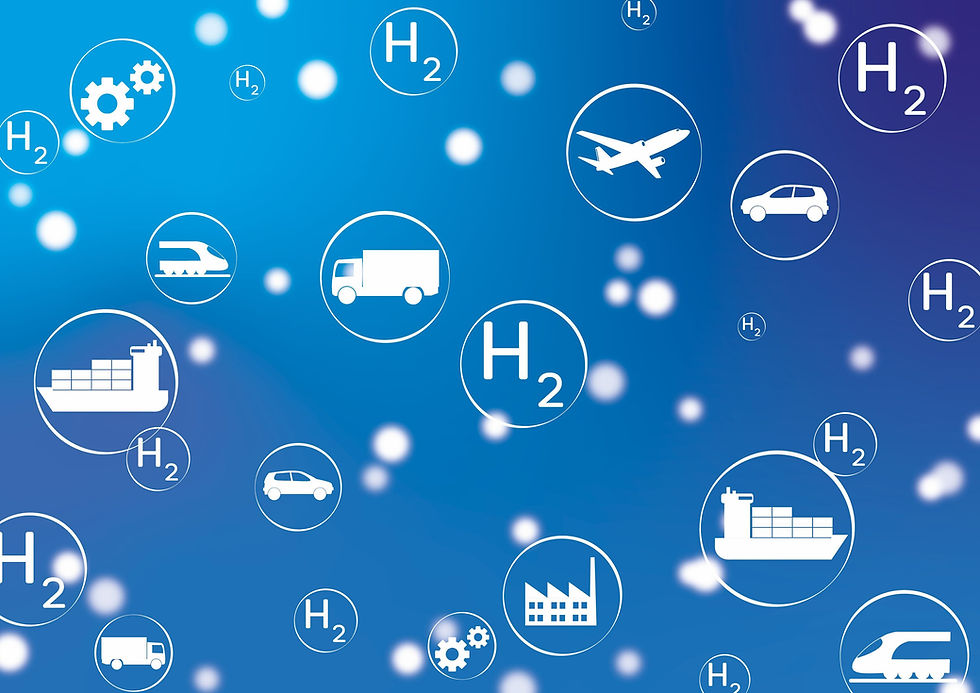
But building hydrogen-powered systems isn’t easy.
Integrating a fuel cell into a vehicle, aircraft, or industrial platform requires the ability to navigate a series of engineering challenges that come with it. High-pressure or cryogenic storage. Complex thermal behavior. Sensitive power conversion Layered control logic. It’s not a plug and play system but rather systems-level thinking from day one of development.
At Motivo, our experience in electrification, vehicle autonomy, , and advanced energy systems has helped us build flexible processes to reduce the risk of t systems integration, especially when deploying new technologies in real world conditions. Whether it’s optimizing system performance across competing metrics, mapping the interfaces between components or identifying hidden failure points, our cross disciplinary teams are built for this kind of challenge.
In particular, Hydrogen systems require precise coordination between mechanical, electrical, and software components. Thermal management, in particular, is a major concern in hydrogen applications. Fuel cells operate best between 60C to 80C, while hydrogen tanks must be stored at either 700 bar (~10,000 PSI) or -253C if liquefied. Auxiliary systems like compressors, pumps, and inverters all generate heat. Managing these thermal loads efficiently is critical for both performance and safety. Furthermore, for airborne applications, the mass of all this additional equipment needs to be minimized to reap the potential kWh/kg benefits of Hydrogen
The path to a hydrogen future is filled with engineering challenges, but that’s where innovation thrives. As the technology advances, success will depend on precise system integration, thermal management strategies, and the ability to move from concept to prototype quickly and effectively.
That’s where Motivo’s rapid prototyping plays a huge role. The ability to move from idea to a physical prototype quickly allows for real world iteration, not just theoretical modeling. Our in-house tools and teams make it possible to test, refine, and validate designs early, before cost, complexity, or supply chain issues get in the way., Hydrogen may be complex but complexity is where we do our best work.