Manufacturing's Robot Revolution
- Motivo
- Feb 13
- 5 min read
Updated: Feb 27
Automation has always been at the heart of manufacturing advancement. Consider the advent of assembly lines in the early 20th century, which revolutionized production by making processes faster, more efficient, and scalable. Now, robotics and automation are driving the next leap forward. By combining advanced robotics with AI, manufacturers are not only enhancing productivity but also solving persistent challenges, from improving product quality to optimizing complex workflows. This synergy is transforming factories into smart, adaptable, and highly efficient ecosystems.
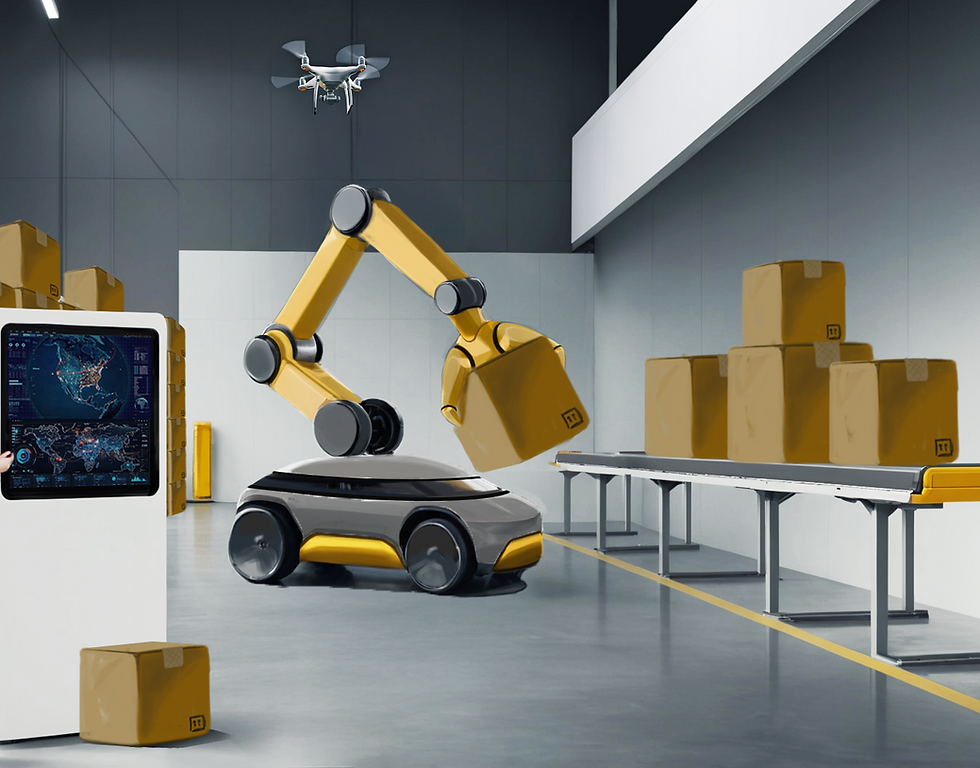
As the pace of technological change accelerates, robotics and automation are reshaping the manufacturing world.
Repetitive Tasks Automated With Precision and Speed
Manufacturing has long relied on repetitive, labor-intensive processes that, while reliable, can stifle advancement and limit efficiency. Tasks like welding, assembly, and inspection demand precision and consistency but are prone to human error and fatigue. Adding to the challenge, these workflows often involve high costs, complex integrations, and a scarcity of skilled labor, which collectively slow down the pace of progress.
By combining advanced robotics with AI, manufacturers are automating repetitive tasks with unmatched speed and accuracy. Take robotic arms like those from GrayMatter Robotics and Path Robotics—they excel at sanding and welding with high precision, improving output while reducing errors. Generative design tools powered by AI are also transforming how parts are designed and optimized for automated production, cutting both costs and time.
Moreover, technologies like computer vision enhance defect detection, allowing robots to identify anomalies in real time. This ensures every product meets exacting quality standards, as seen in solutions by Autumn Labs. With automation, manufacturers can break free from inefficiencies and shift focus to high-value advancements.
So, how can companies embrace automation without overhauling their entire system? The rise of Robots as a Service (RaaS) provides a scalable solution. By outsourcing robotic capabilities, businesses can access cutting-edge technology without the heavy upfront investment, lowering barriers to entry and unlocking automation's potential.
Managing the Technical Challenges of Robotic System Design
Building and maintaining a robotic system—especially at a fleet level—requires balancing complex design trade-offs that impact performance, scalability, and reliability. System designers must integrate both hardware and software seamlessly to achieve efficient automation. On the hardware side, choosing the right end effector is critical, as tasks like precision welding, high-torque assembly, and delicate material handling demand vastly different grippers. Some applications require soft robotics for gentle handling, while force feedback sensors improve adaptability by allowing robots to adjust grip strength dynamically.
Software is equally crucial. Advanced motion planners and real-time control systems must process dynamic feedback to optimize trajectories and prevent collisions. Many robotic systems rely on the Robot Operating System (ROS) for modular development, but integrating ROS with proprietary manufacturing platforms presents compatibility and real-time performance challenges. Managing a fleet of robots also demands a robust telemetry pipeline for performance monitoring, predictive maintenance, and remote diagnostics. Overcoming these challenges requires deep expertise in robotic architecture, AI-driven optimization, and scalable software frameworks—ensuring automation delivers not just efficiency but long-term reliability and adaptability.
So, how can companies embrace automation without overhauling their entire system?The rise of Robots as a Service (RaaS) provides a scalable solution. By outsourcing robotic capabilities, businesses can access cutting-edge technology without the heavy upfront investment, lowering barriers to entry and unlocking automation's potential.
Simplified Integration Through Collaboration and Flexibility
While the advantages of robotics in manufacturing are clear, integrating them into existing workflows presents significant challenges. Many production processes are deeply entrenched, and the upfront costs of automation can be a major barrier. Additionally, a shortage of skilled labor for programming and managing robotic systems further complicates adoption.
Collaborative robots, or cobots, help bridge this gap by working alongside human operators. Unlike traditional industrial robots, cobots are easier to program and operate, making them an accessible entry point for manufacturers hesitant to commit to full automation. Meanwhile, upskilling initiatives are equipping workers with the knowledge needed to manage robotic systems, fostering a seamless transition from traditional to automated workflows.
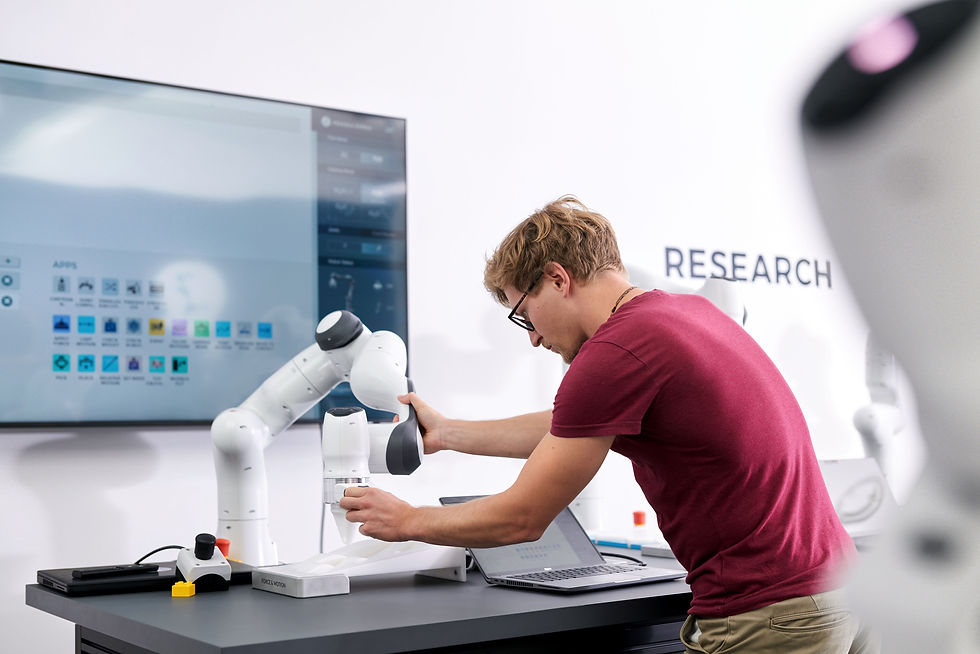
Further advancements, such as soft robotics and swarm robotics, are enhancing flexibility in manufacturing. These technologies allow businesses to scale automation incrementally, reducing risk while maximizing returns.
This spirit of innovation extends beyond manufacturing into industries like agriculture. A prime example is the German company Organifarms, founded in 2021 with a mission to revolutionize fruit and vegetable harvesting through efficiency, sustainability, and cost-effectiveness. Their flagship product, BERRY, is a strawberry-harvesting robot equipped with a Franka Robotics arm mounted on an autonomous mobile platform powered by intelligent software.
BERRY not only addresses labor shortages but also supports sustainable harvesting practices, demonstrating how robotics can drive efficiency and sustainability across industries.
Unlocked Creativity By Breaking Down the Cycle of Sameness
Manufacturing has often been caught in the “sea of sameness,” where sticking to tried-and-true methods feels safer than exploring new territory. Originality, while valuable, is costly—prototype development, testing, and scaling for edge cases require significant resources. This is especially true in the high-stakes world of industrial manufacturing, where the margin for error is slim.
Generative AI and embodied AI are enabling designers to rapidly create and iterate on virtual prototypes. These tools lower costs and reduce the time needed to experiment, making it easier for manufacturers to explore edge-case scenarios. For instance, startups like Pivot and GrayMatter Robotics are leading the charge in applying AI to custom manufacturing processes, bridging the gap between creativity and feasibility.
Smart factories inspired by leaders like Tesla showcase how a blend of robotics, AI, and data analytics can transform production. Autonomous manufacturing lines that adapt in real time are no longer a distant dream—they’re being built today. This shift isn’t just about efficiency; it’s about unlocking entirely new possibilities for product differentiation.
Scalable Personalization Without Sacrificing Efficiency
Today’s manufacturing world is under pressure to deliver customized solutions without sacrificing speed or quality. Whether it’s designing unique parts or accommodating specific customer needs, traditional processes struggle to keep pace with this demand.
By leveraging domain-specific large language models and real-time analytics, manufacturers can integrate customer specifications seamlessly into automated workflows. Autonomous systems are now capable of on-demand customization, such as producing custom-printed PCB boards or tailored metal components.
For example, robots equipped with AI can replicate high-skill tool knowledge, putting years of tribal expertise at the operator’s fingertips. This not only increases efficiency but also democratizes access to advanced manufacturing techniques, opening doors for smaller shops to compete on a larger scale.
What’s Next?
The future of robotics in manufacturing lies in pushing boundaries even further. Emerging trends like embodied AI, humanoid robots, and autonomous mobile robots are poised to tackle increasingly complex tasks, from real-time decision-making to fully autonomous factory operations. As these technologies mature, they will reshape manufacturing into a smarter, more adaptable, and more inclusive industry.
Accessibility has long been a driver of innovation, and robotics is proving that the same principle applies to manufacturing. By combining advanced technologies with human ingenuity, the industry is breaking free from old limitations to create smarter, more sustainable solutions. The question isn’t if robotics will drive manufacturing’s robot revolution—it’s how quickly you’ll see the results.